Our Services
Brochure
Download our document to see specific data of the service and how we work.
Let’s Start Work
Together
Dwija Inc is the leading solution provider for the steam, thermic fluid and hot water application. Trust in our expertise & commitment to excellence.
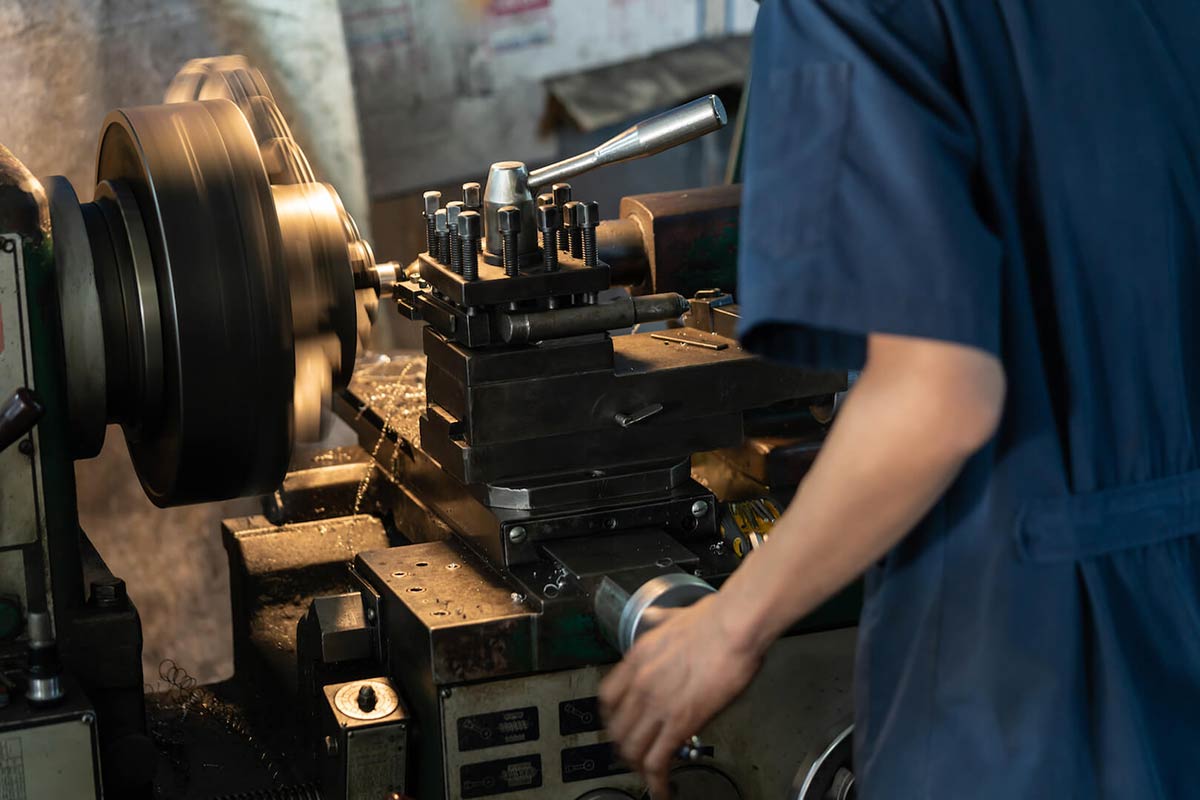
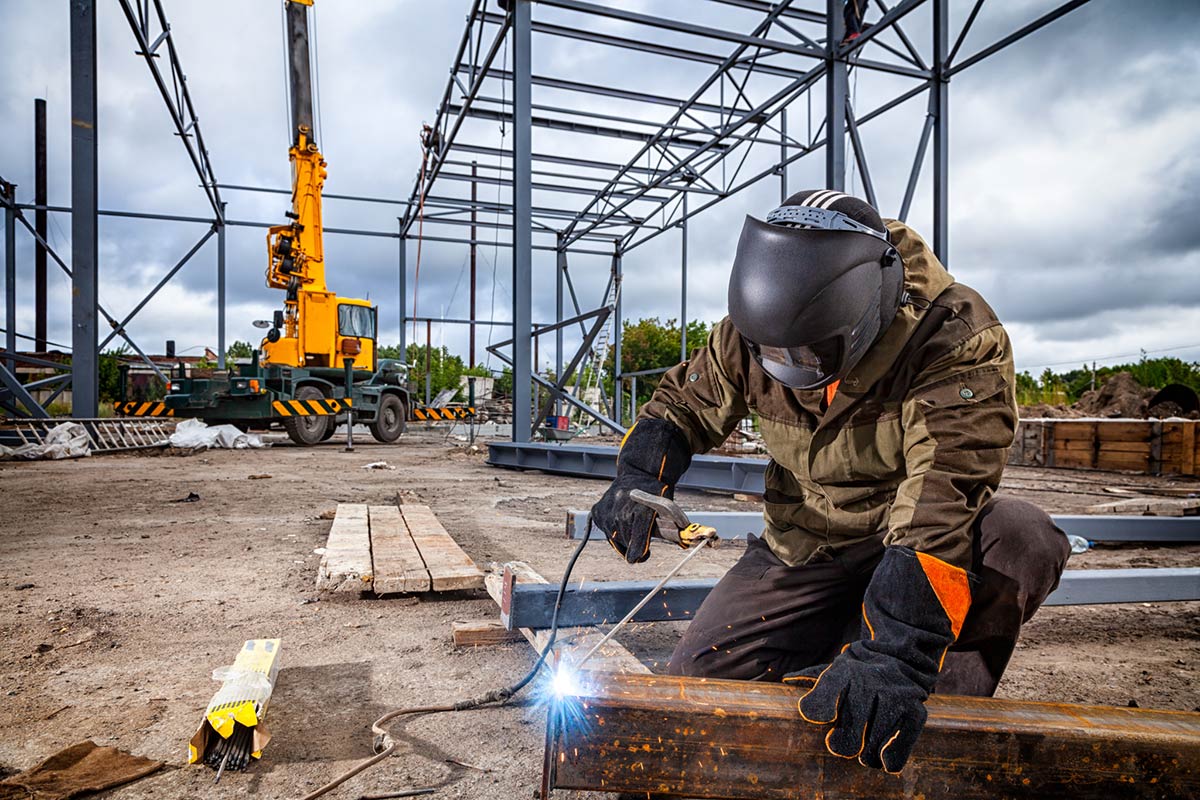
Thermic Fluid Application Design Services
Scope evaluation – Data and Drawings study at particular heat exchanger user sections Develop Thermic Fluid distribution, handling & heating scheme.
- Study the specifications & drawings of the heaters and Balance of plant area. Review proposed layout & location of the various equipment connected to the TF system and routing of its piping.
Compile data, drawings, specification etc. on the individual production equipment & assess their heat exchanger requirements of TF flow, TF temperature, TF pressure loss, TF volumetric holdup etc.
- Design and review of specifications and construction drawings of each production machines.
- Estimate the heat demand pattern for proposed production equipment based on production rates, operating temp., seasonal changes, cycle time, pipe connection size etc. of individual equipment
- Design of optimum Thermic oil distribution & handling scheme to match the generation, distribution & application of heat for integrating the various components on the heater section and production equipment.
Design & sizing of necessary secondary thermic oil booster pumps for the production equipment’s, to match the requirements of the heat transfer equipment’s being provided by equipment vendor.
- Design & sizing of various accessories of the TF system like pump/s, expansion tank, deaerator cum cooler unit, piping, valves (automatic & manual) & instruments (pressure, temperature, level, flow etc.)
- Prepare piping and instrumentation diagram (PID) of the proposed TF heating system.
- Sizing, design & prepare basic G.A drawings of: –
a) Expansion tank
b) Deaerator vessel
c) Cooler vessel
d) Receiver (overflow) tank.
e) Degasser pots
- Design of expansion U-loops. Advice on location, elevation of accessories like pumps, expansion tank, deaerator unit, cooler unit, receiver tank, pipe routing, piping expansion loops etc.
Review / design of TF flow regulating systems for heater including selection of flow sensing devise, DP transmitter, PID controller, 2-way control valve.
- Design of basic scheme for measuring instantaneous heat output from heater & also for totaling daily heat energy generation Prepare schematic piping layout diagram for the proposed system.
- Prepare detailed specifications for major brought out components of the system Technical scrutiny of offers from vendors Provide technical support via telephone, email, WhatsApp etc. during installation & trial runs of upgraded Thermic fluid system.
Outdoor visits for discussion, collecting data, inspection & trial runs in-connection with the assignment.
Hot Water Application
Study drawings & specification of the production Equipment’s Assess heat demand, Hot water temp., flow, pressure drop, volumetric capacity etc., for above production equipment, based on the process parameters like speed, moisture etc.
- Review Sizing of the Hot water generator, based on the heat load estimation & practical figures obtained from client on the existing fuel consumption which is currently used for existing production line. Review drawing, documents of the above Equipment’s & give suggest modifications, as required. Design optimum Hot water distribution & handling scheme, to match the generation, distribution & application of heat for proper integration of the various components in the heater section & production section.
- Design & sizing of Hot water secondary booster pump, to match the high flow, lower temp., pressure drop requirements of the production machine.
Estimate Hot water hold up volume of the system & pressure drop for the proposed piping. Design scheme of using N2 gas for pressurizing expansion vessel of PHW system. Sizing of N2 gas train, safety valve, vacuum breaker, back pressure regulating valve etc. Along with instruments to be mounted to be mounted on expansion vessel, for monitoring & control of Pressure, level & temperature of water in the expansion vessel. Advice on quality of treated (soft, Oxygen free etc.) feed water to be used in PHW system design scheme for supply of treated water from feed tank to expansion vessel & prepare P&I diagram of proposed PHW system with basic GA drawings for,
A) Expansion vessel
B) Feed water service tank
C) Deaerator unit
D) Degasser pot & Advice on location, elevation of new accessories like expansion vessel, deaerator unit, pumps, feed tank, N2 train & routing of PHW piping.
- Design of expansion loops on the Hot water pipe routes Design & preparation of piping and instrumentation (P&I) diagram of the proposed integrated Hot water line heating system Prepare specifications for major brought out components required for the system.
Steam Application
- Study process line with each equipment’s heat load and maximum Temperature requirement.
- Steam line sizing based on steam flow rate, Pressure, Temperature, Dryness fraction, piping length, pressure drop and velocity
- Design integrated solutions for Steamline Accessories like:
- Pressure Reducing Stations
- Pressure Reducing & De-superheating stations
- Condensate Recovery Systems
- Steam Traps (Thermodynamic, Ball float, Bimetallic, Thermostatic)
- Disc-check Valves, Air vents, Vacuum breakers
- Moisture Separators, strainers
- Level gauges & controls
- Condensate line sizing and designing of steam trap modules and air vent assembly Flash steam recovery solutions Condensate recovery based on various methods like direct Traps, steam operated condensate pumps or Electric pumps etc. Design for Deaerator head and Boiler feed water tank.
What is Included
Flow system design involves the engineering and optimization of systems that control the flow of fluids, gases, or substances in various industrial processes. It includes the selection of appropriate components, system layout, fluid dynamics analysis, and control system design to ensure efficient and reliable flow.
Flow system design is essential for achieving optimal performance and efficiency in industrial processes. It ensures the proper control of flow rates, pressures, and temperatures, leading to improved productivity, energy efficiency, and operational reliability. A well-designed flow system minimizes losses, enhances process stability, and reduces downtime and maintenance costs.
everal factors are considered in flow system design, including: - Flow rate requirements - Pressure and temperature specifications - Fluid properties (viscosity, density, corrosiveness) - System layout and space constraints - Safety regulations and standards - Energy efficiency goals - Maintenance and accessibility requirements
The flow system design process typically involves: - Understanding the requirements and objectives - System layout and component selection - Fluid dynamics analysis and optimization - Control system design and instrumentation - Safety considerations and compliance - Testing, validation, and optimization
Flow system design often utilizes specialized software and tools such as computational fluid dynamics (CFD) simulations, piping design software, and process simulation software. These tools help analyze fluid behavior, simulate system performance, and optimize the design for efficiency and reliability.